モノづくりの未来を見据えた当工場では、生産性の向上、省力化、省人化に取り組んでおります。
さまざまアイデアと工夫を駆使し、効率的で持続可能な生産体制を実現しています。
私たちの取り組みをぜひご覧ください。
さまざまアイデアと工夫を駆使し、効率的で持続可能な生産体制を実現しています。
私たちの取り組みをぜひご覧ください。
POINT
1

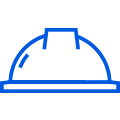
作業者の負担・安全性を
重視した搬送ラインの導入
重視した搬送ラインの導入
光子局の組立配線作業を行う組立搬送ラインを導入しました。
製品の移動を電動による自動搬送とすることで、
作業者の負担を軽減します。
製品の移動を電動による自動搬送とすることで、
作業者の負担を軽減します。
POINT
2

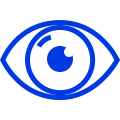
生産現場の見える化
生産ラインに「生産進捗表示パネル」を導入し、進捗状況を見える化しました。
関連ポイント!
全自動圧着機
プログラム式ワイヤーツイスター機
全自動防湿塗布装置
STEP
01
作業Aライン
製品のケースにプリント板やスイッチ等を容易に取付けするため、昇降する機構を設けています。
また、組立手順やベテラン作業者の動きを記録した動画マニュアルをタブレットで確認しながら作業を行うことで、
作業員の作業レベルの均一化を図っています。
また、組立手順やベテラン作業者の動きを記録した動画マニュアルをタブレットで確認しながら作業を行うことで、
作業員の作業レベルの均一化を図っています。
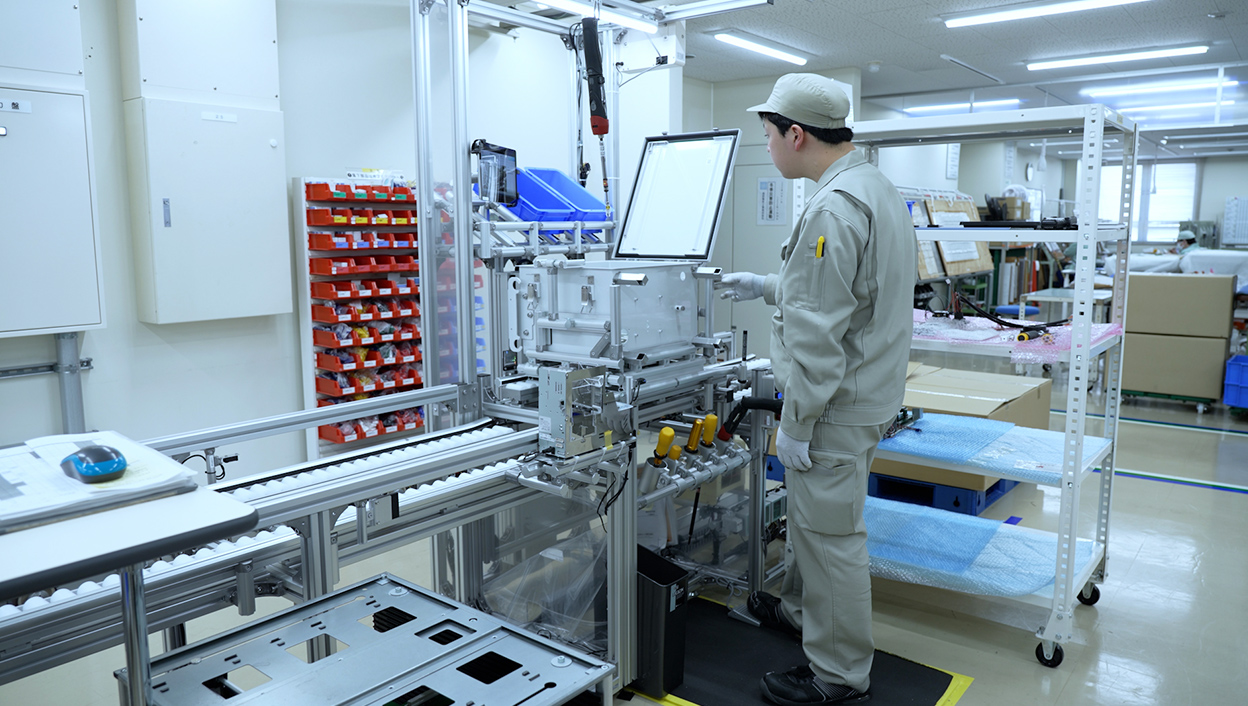
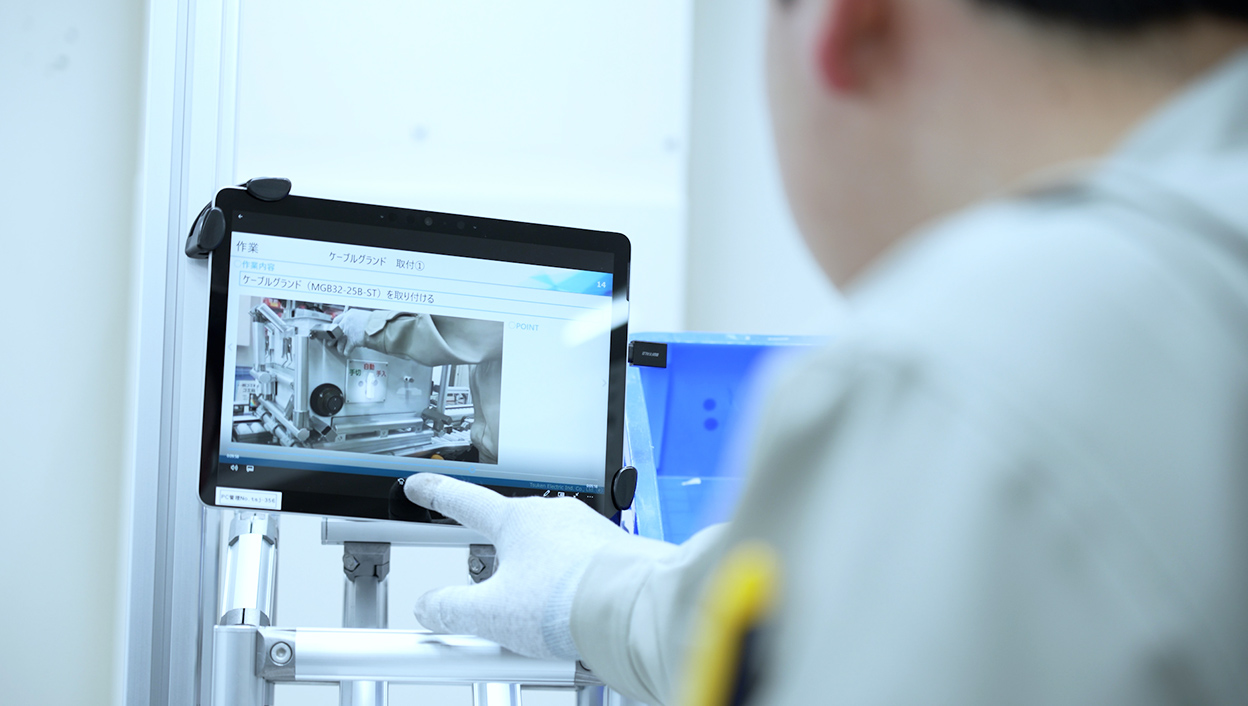
STEP
02
作業Bライン
作業Aラインから自動搬送された製品を足元のペダルで倒し、作業しやすい角度に調節します。
プリント板を手順どおりに実装し、電動ドライバで固定していきます。
プリント板を手順どおりに実装し、電動ドライバで固定していきます。
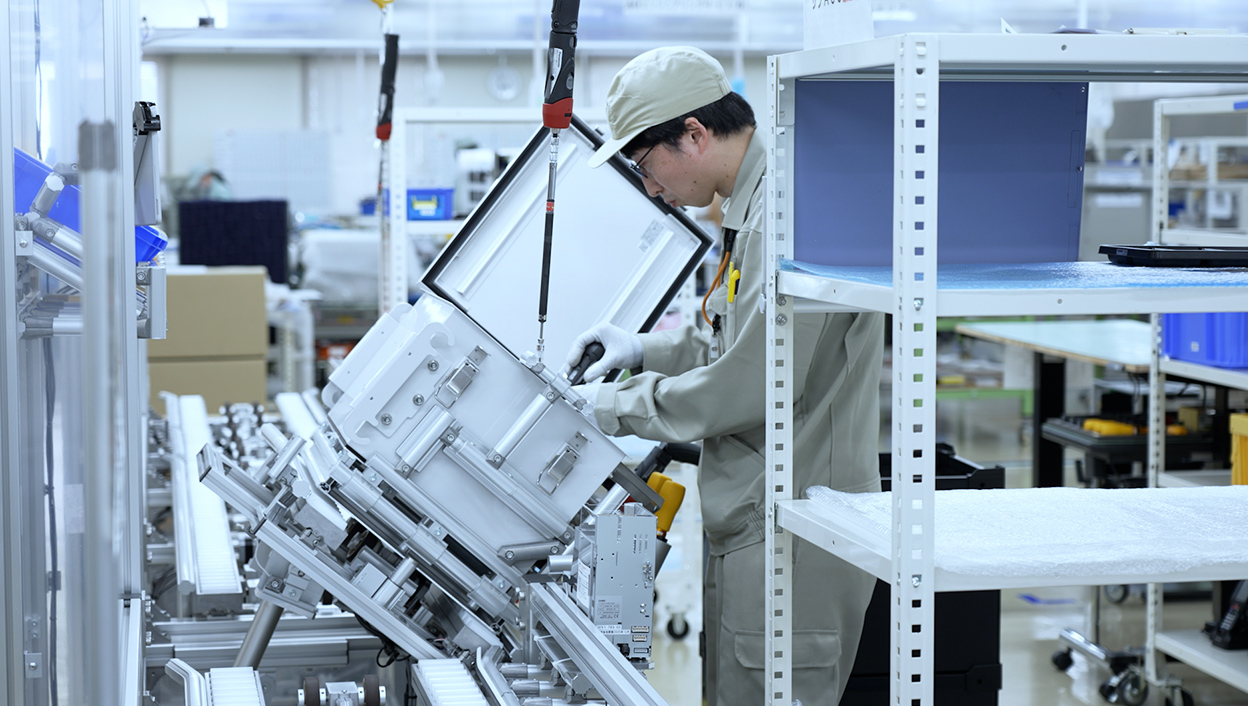
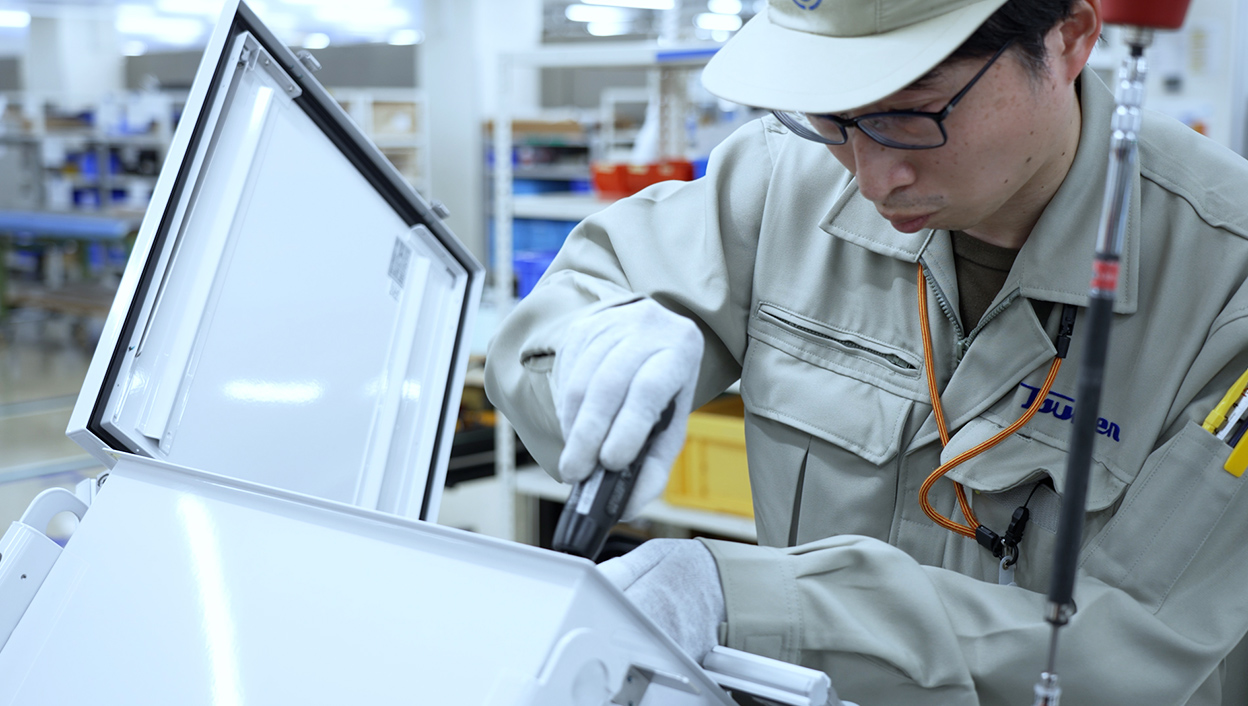
STEP
03
調整・計測ライン
必要とする部品とプリント板を取り付けた製品に対して調整・計測試験を行います。
絶縁耐圧試験や単体動作試験など各種試験を行い、合格品は次の工程に進みます。
絶縁耐圧試験や単体動作試験など各種試験を行い、合格品は次の工程に進みます。
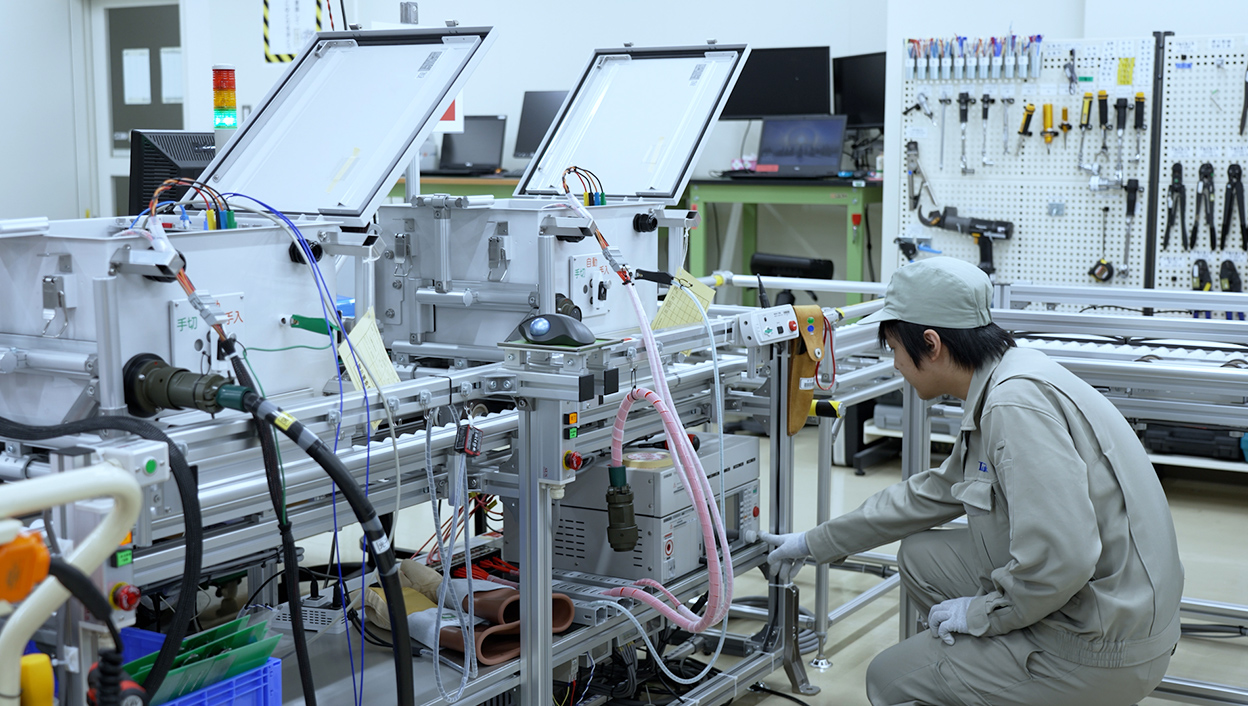
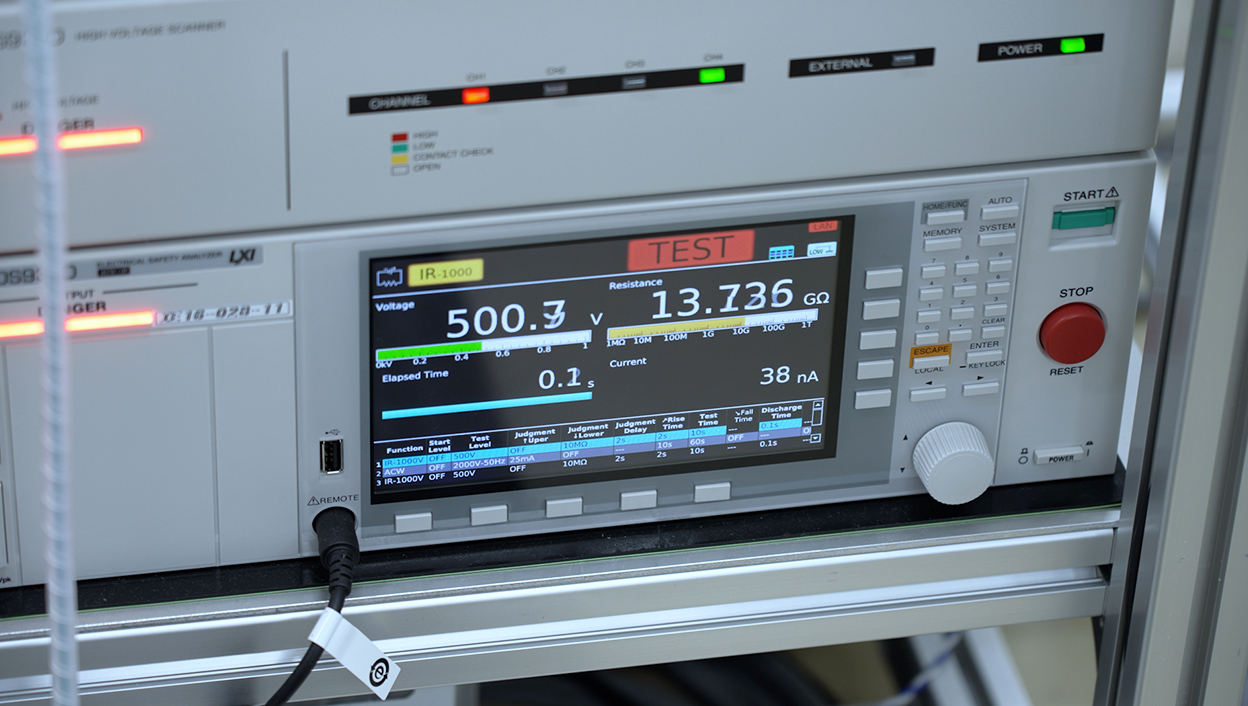
STEP
04
エージングルーム
調整・計測試験が完了した製品は、エージングルームに運ばれます。
エージングルームでは、製品出荷前の試験として一定の高温環境下にて長時間連続運転による耐久試験を行います。
エージングルームでは、製品出荷前の試験として一定の高温環境下にて長時間連続運転による耐久試験を行います。
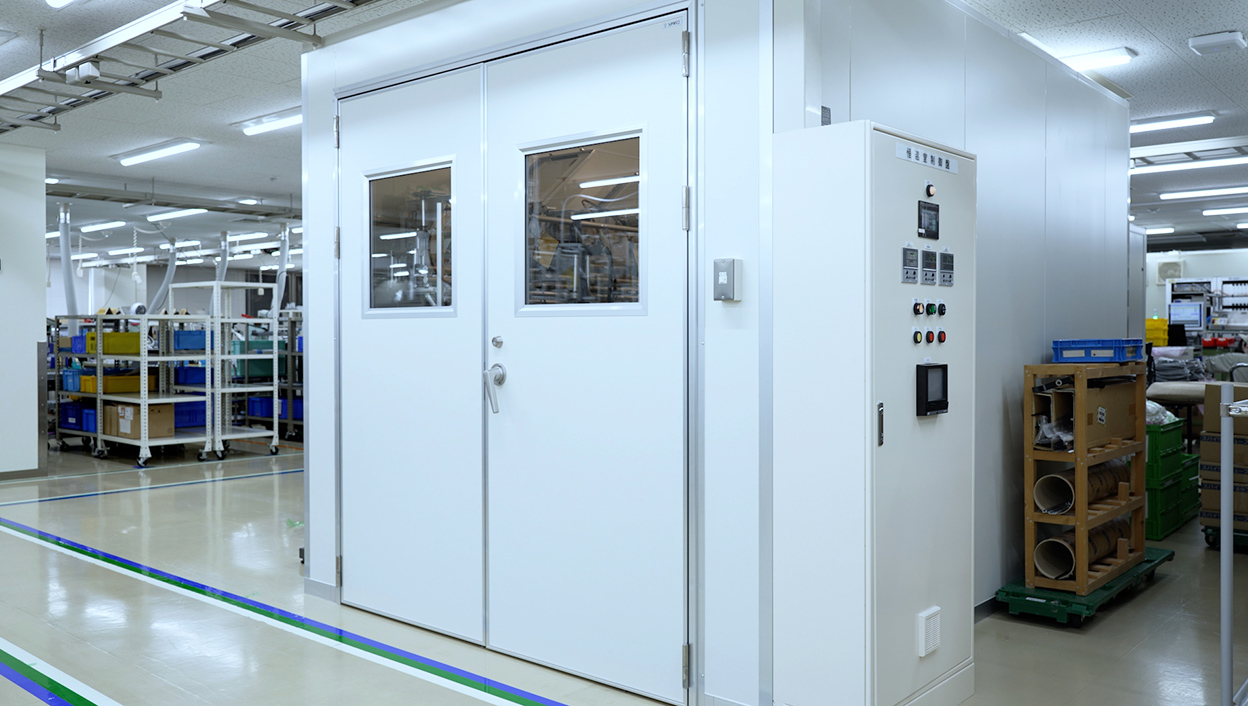
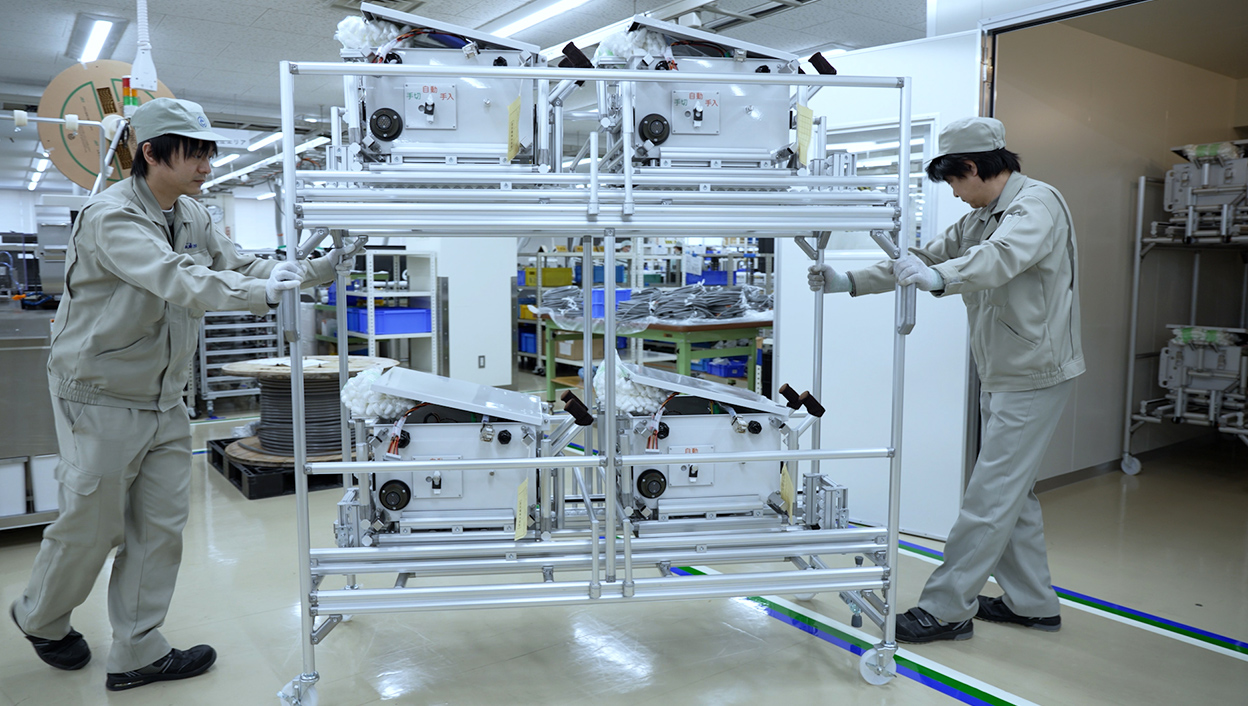
STEP
05
梱包ライン
製品の梱包作業における作業者の負担を低減する目的として、梱包ラインを導入。装柱用ボルトの取り付け、最終外観検査を行います。
電動ウインチで製品を吊り上げ、段ボールへの収納をアシストします。
電動ウインチで製品を吊り上げ、段ボールへの収納をアシストします。
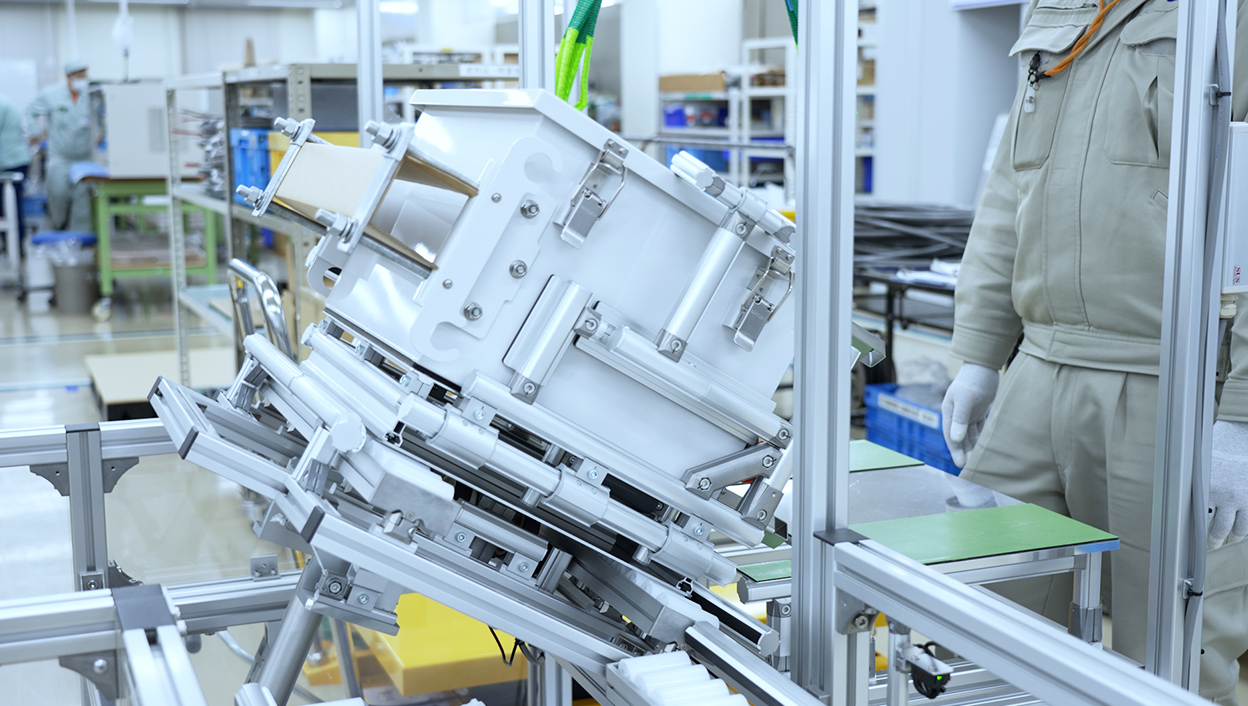
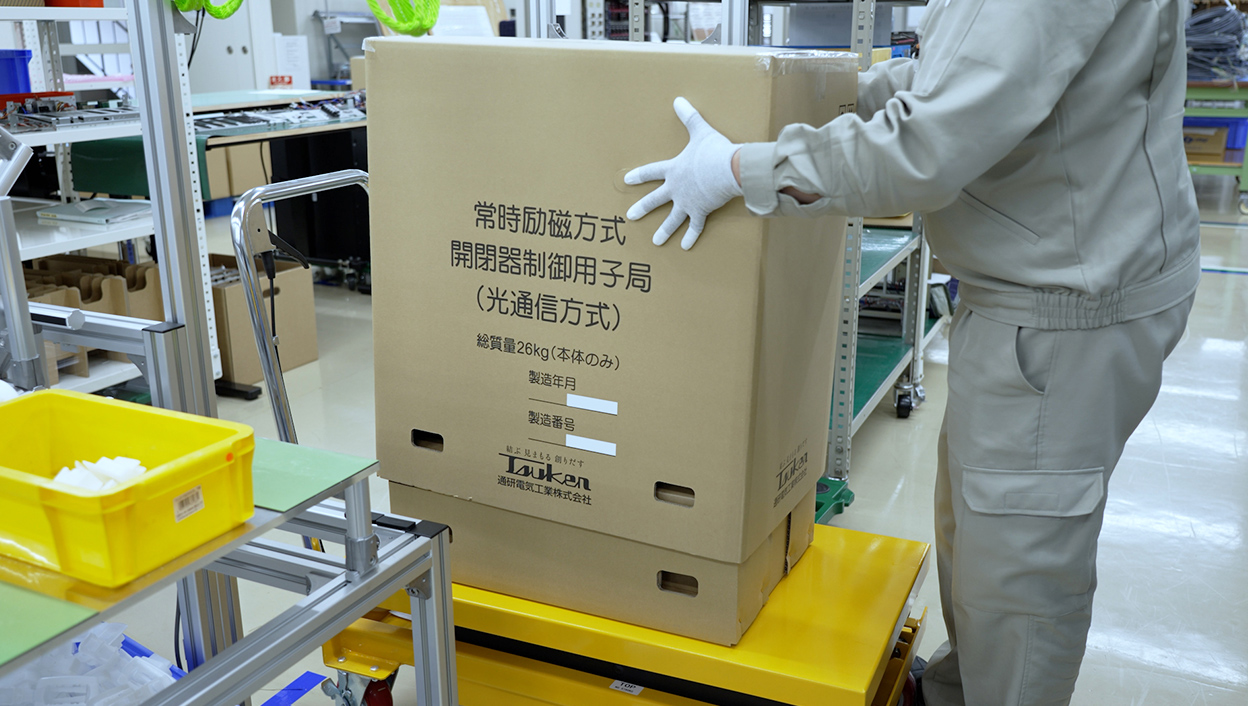